We made it back to Waltham with all the parts we collected a couple days later. I took the dune buggy in and enjoying the nice weather.
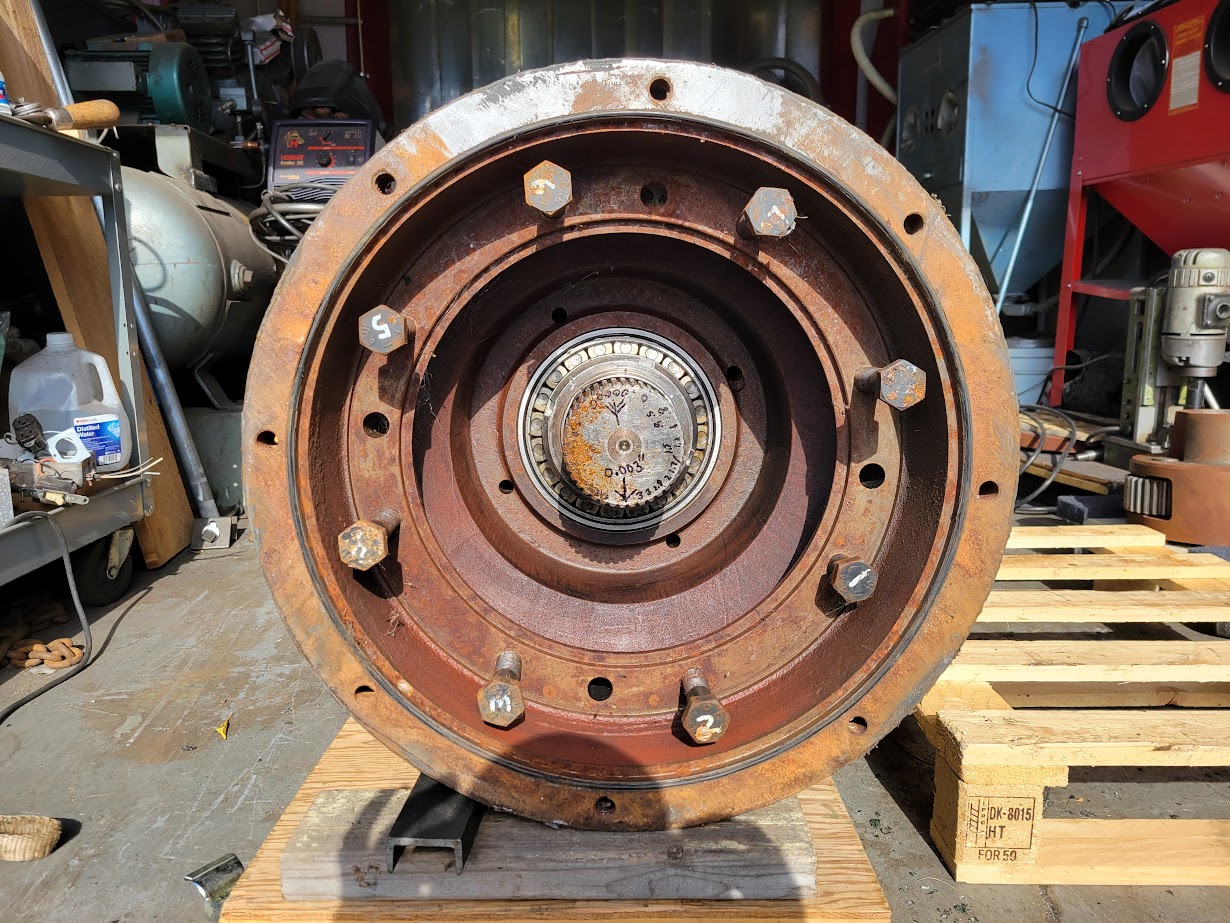
Here is the first piece of the puzzle, the giant 205mm taper roller bearing assembly. When designing turbines, it seems like the design life is 100 years underwater. The turbine can't dissolve in 10 years, so you have to make everything thick enough for it to have a useful service life. The bearing assembly is a mix of welded and turned parts all about min thickness 12mm so this small assembly is easily 400lbs. You can see a bunch of ancient hyroglyipics from the previous people who took it apart, what they mean? No idea.... The large m20 bolts I assume match up to the planet gear in a certain orientation but with no manual or instructions your guess is as good as mine.

There are two types of people in the world, there are those that sees something working and says thats great. Then there are people where they see something and they say I can make this better or fix that. In my experience the latter person doesnt fundamentally understand what has gone into that process in order for it to work. When you are working on something that was not designed by you nor do you have any instructions, documentation, or a company to call you have to take great care in documenting what you do. The first thing we wanted to check was the condition of the main taper roller bearings. Luckily all of the special wrenches that have been made over the past 40 years stayed with the turbine. You can see this giant 4'' steel pipe had some tangs welded on it and a nut to turn it. This allowed a person to set the preload for the bearings.
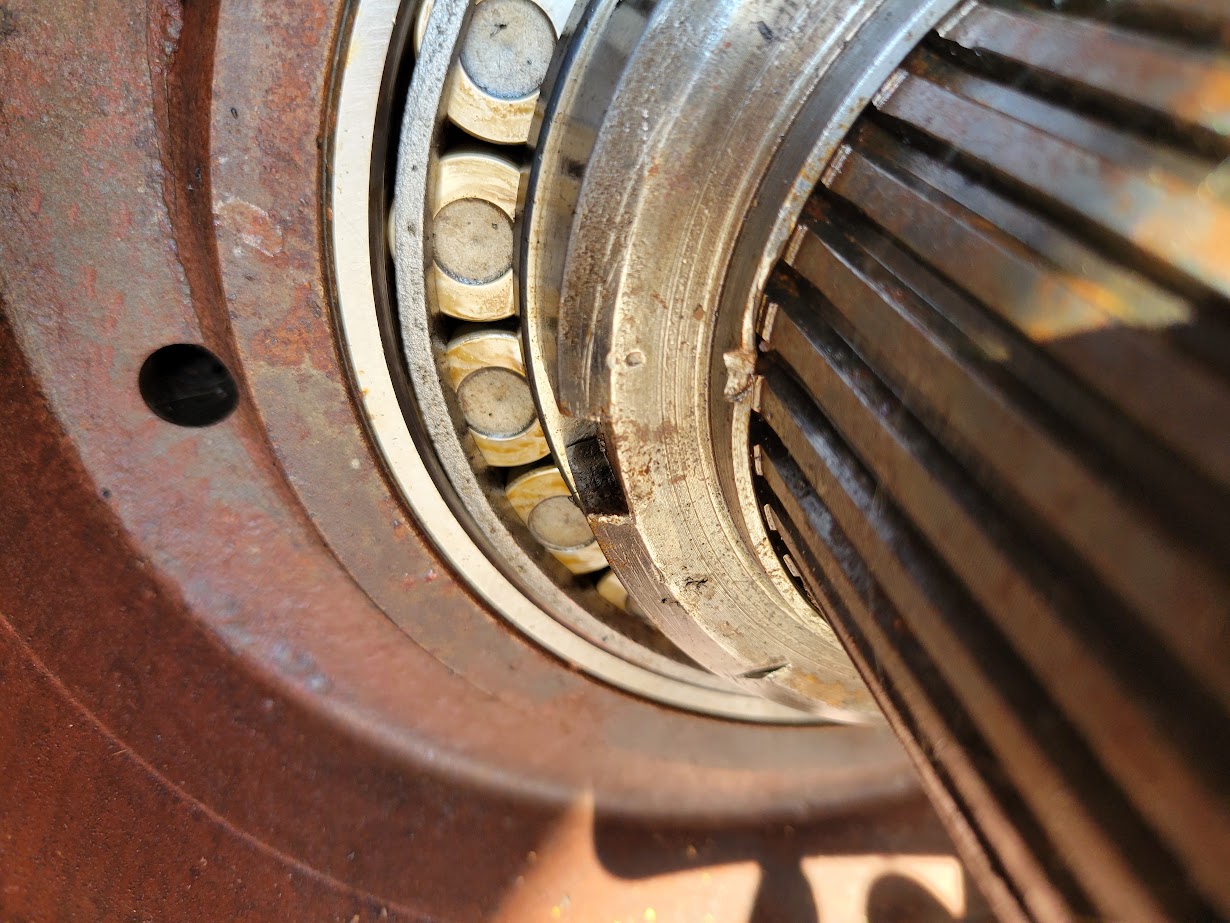
After a short time of setting up enough strap wrenches and trying to see if this big nut or retaining nut would move, I noticed that the previous owners had swadged the nut onto the shaft. This is a good idea in a vibrating system as this nut could loosen over time, and this little ping in the nut jams it in place. After this discovery we had to sit back have some wine and think, do we really need to take off this nut? Assuming the previous installers figured out the preload and set everything up correctly it should be good. The turbine ran for four years before taken offline, so we decided to inspect the rollers and bearing race and clean it and call it a day.
After cleaning the bearings and thinking about how can we make sure that they have the correct preload, we came up with a cute idea. Through the power of math, we can deduce the theoretical torque required to spin the bearings. We know the diameter, surface area, and approximate preload. With a rope tied around the shaft with a diameter of 4'' and a scale, we can see it took about 6lbs. According to Austin this was within spec.
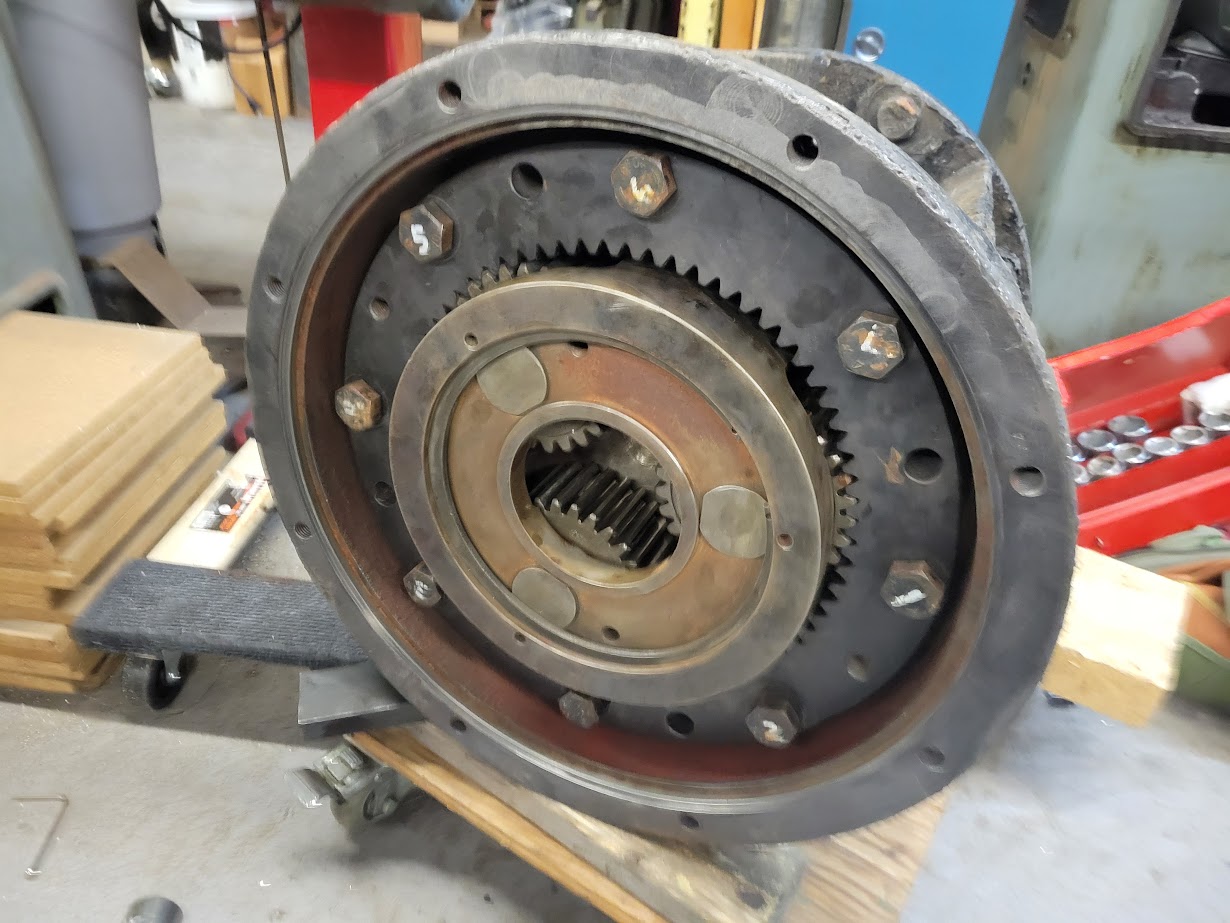
Here is the planetary installed onto the bearing shaft. It took some cleaning up of the splines to get it on but it just schlooped on. Again, this is something that we decided was in good shape and cleaned it oiled it and threw it back in. This particular planetary was painstakingly rebuilt by French River Hydro. All of the needle bearings were bad, and they found Dowel stock of the same diameter, and made new needle bearings, a extremely tedious process. The planet gear bolted to the bearing housing was extremely hard, to the point that a new Nicholson file skated right across the surface not leaving a mark. Everything was bolted up and torqued. This assembly was happy, onto the next!
You can see it spins very nicely, almost like someone made it that way! Ha. A small step for turbine, large leap for turbine go Brrrrrr.
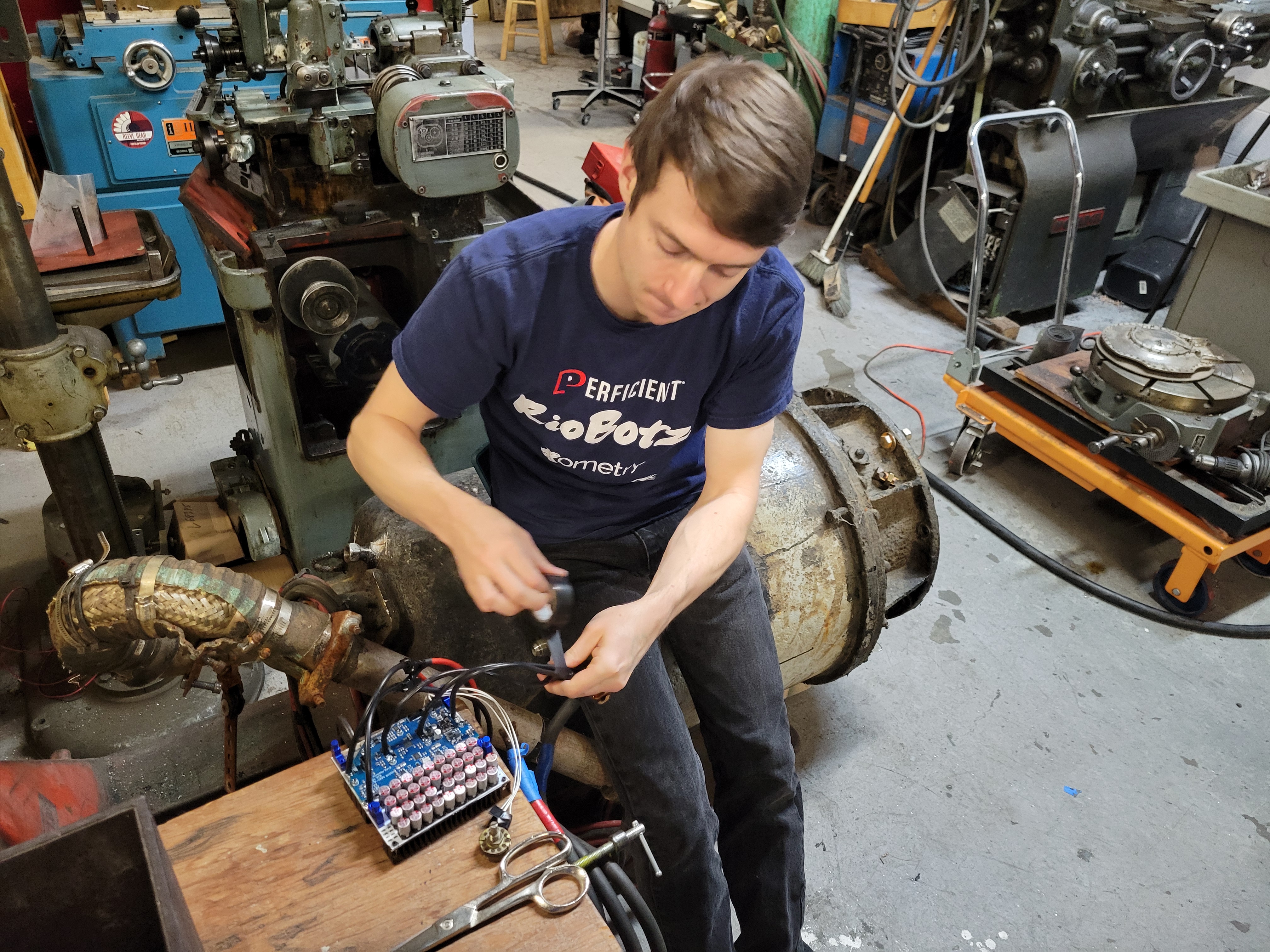
Next up is a test to make sure the motor "generator" is working and happy. We checked the resistance phase to phase, and phase to ground, and everything looks good. We were slightly worried about using a Megger because, while the motor isnt shorted we werent sure how the insulation is. Remember that the motor spins at 1800rpm submerged in oil, and you can bet your ass its watching you whip, and nae nae. We postulate that one reason for the motor to short out is that the insulation eventually wears of somehwere from cavitation and shorts. So here we have Austin hooking up a homegrown motor controller to test the motor.
The test we are doing here is simulating the motor under full load. One idea we had to pick up some efficiency was to run the motor in air rather than oil and grease the bearings. This proved to be too difficult but we wanted to test the motor anyway so it was a good excuse. To simulate this full load situation Austin took a bucket of amps, and slowly poured them into the motor, while spinning it slowly.
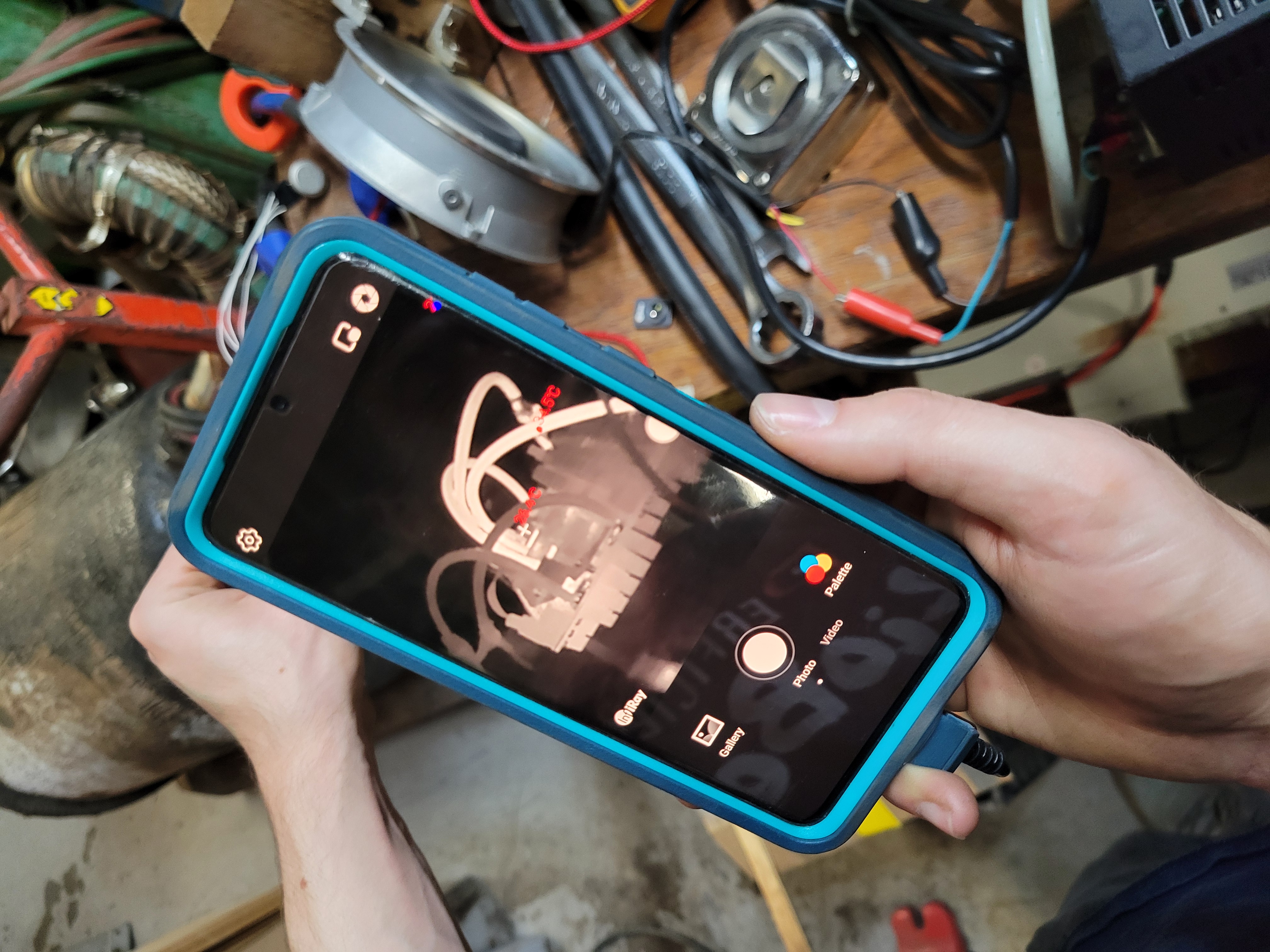
You can see austins motor controller wires are getting warm but his controller is cool, i'd say thats pretty cool...
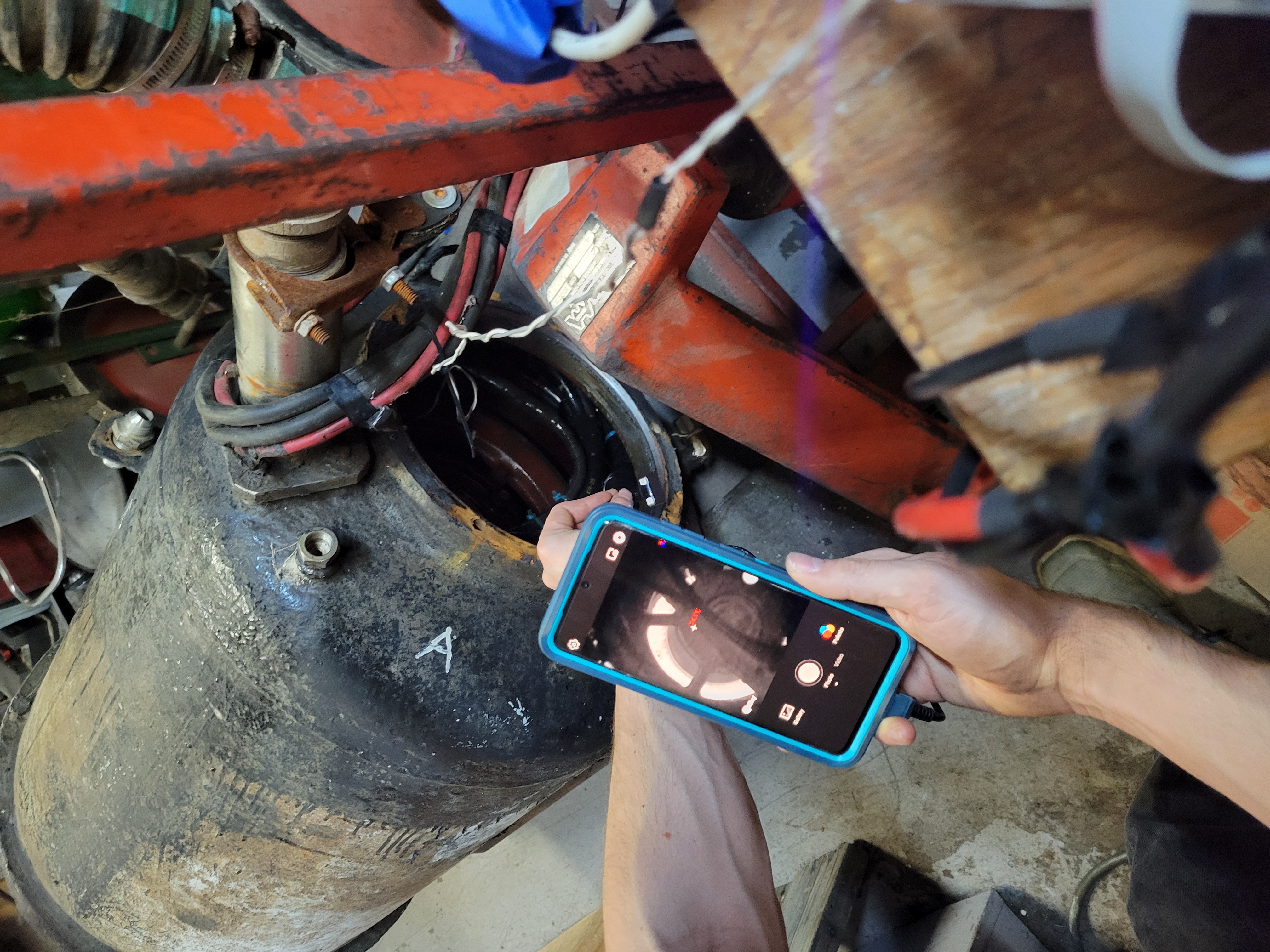
You can see with the thermal camera, the motor windings getting warm. Another reason for doing this test was to drive any moisture out of the motor housing before its sealed up. It has been sitting outside under a tarp for some time. I think we brought the windings up to 50c or so and everything seemed to check out. Now that we have the planetary and the motor in a known condition we can start to assemble more of the puzzle. So far so good!Next up is fixing the Achilles heel of this turbine, well one of them.